Automated Storage and Retrieval Systems (AS/RS) are a cornerstone of modern warehouse automation, significantly enhancing efficiency and space utilisation. Once considered a complex and expensive investment, advancements in AS/RS technology and diverse options have made these systems increasingly accessible for various operations across a range of industries and business sizes. Understanding what AS/RS is and the types of AS/RS available is crucial for choosing the best solution to meet specific warehousing needs.
What is AS/RS
AS/RS is a technology that automates the storage and retrieval of items in a warehouse. AS/RS systems use computer-controlled equipment to move items to and from storage locations, improving efficiency and accuracy. Here are several examples of automated storage and retrieval systems that demonstrate the diverse applications and technological advancements within this field:
Vertical Lift Module (VLM) AS/RS
Vertical Lift Module (VLM) AS/RS is an enclosed system featuring an inserter/extractor device that moves vertically between columns of trays. These systems automatically retrieve and deliver trays to operators at an access opening, facilitating efficient order fulfilment. VLMs can be configured with either fixed or dynamic tray storage.
This type of automated storage and retrieval system offers fixed and dynamic configurations. Fixed systems maintain a consistent tray location, while dynamic systems optimise tray storage based on usage frequency.
Micro-Load Stocker AS/RS
Micro-load stocker AS/RS is designed for the automated storage and retrieval of individual totes or cartons. These systems are commonly used for buffering, sequencing, and managing point-of-use items. Micro-load systems can be integrated with other AS/RS systems to improve overall performance and reduce space requirements. They are a good example of an automated storage and retrieval system designed for smaller goods.
Vertical Sequence Module (VSM) AS/RS
Vertical Sequence Module (VSM) AS/RS, a specialised type of automated storage and retrieval system, is designed for high-density buffering and tote sequencing. These systems store and retrieve totes in a specific sequence as required, ensuring that items are available in the correct order for downstream processes. VSMs can be integrated with conveyors, AMRs, other AS/RS systems, or manual pick windows to create highly efficient workflows.
Unit-Load AS/RS
Unit-load AS/RS is designed to handle large, heavy loads, such as pallets and cases, within a warehouse environment. Unit-load AS/RS is ideal for situations with limited pallet storage space and critical retrieval needs.
Fixed-Aisle Unit-Load AS/RS Crane
Fixed-aisle unit-load AS/RS cranes operate within pallet racks with narrow aisles. The crane is fixed to a single aisle and moves vertically and horizontally within that aisle to retrieve and store loads. This type of automated storage and retrieval system is particularly useful for industries with high throughput and stringent inventory control, like pharmaceuticals, where rapid and precise access to palletised goods is essential for just-in-time manufacturing or distribution.
Moveable-Aisle Unit-Load AS/RS Crane
Moveable-aisle unit-load AS/RS cranes are similar to fixed-aisle systems, but the crane, a sophisticated piece of warehouse technology, can move between aisles. This allows a single crane to service multiple aisles, increasing efficiency and reducing the number of cranes required. This configuration is most useful in warehouse environments where flexibility and cost-effectiveness are paramount, such as in large distribution centres with fluctuating inventory levels or when handling seasonal product lines.
Mini-Load AS/RS
Mini-load AS/RS is designed for smaller loads, such as totes, trays, and cartons. These systems are suitable for operations with a large number of SKUs and limited floor space, making them ideal for e-commerce fulfilment centres and parts distribution. This warehouse technology is often used for buffering, sequencing, and replenishing pick locations, ensuring efficient order processing and reducing the time spent searching for items. They are also useful for managing slow-moving inventory within a warehouse to maximise space.
Shuttle-Based AS/RS
Shuttle-based AS/RS uses shuttles or bots that travel on tracks within racking structures to deliver inventory. Shuttles retrieve and deliver totes or cartons to workstations, improving efficiency and reducing travel time. Different shuttle models, with varying designs and benefits, are available, such as vertical orientation and independent delivery.
Pallet Shuttle AS/RS
Pallet shuttle AS/RS is designed to automate the storage and retrieval of pallets within racks. Three primary types exist: 1D, 2D, and 3D pallet shuttles. These systems are suitable for high-density pallet storage in various environments, including ambient, cold, and frozen. Various equipment, such as shuttle carts, Autonomous Mobile Robots (AMRs), Automated Guided Vehicles (AGVs), forklifts, and elevators, can be used in conjunction with pallet shuttle systems.
Autonomous Mobile Robot (AMR)-Based High-Density AS/RS
AMR-based high-density AS/RS uses AMR robots that travel vertically on storage racks within the warehouse to retrieve totes or cases. The AMR stores inventory, navigates to workstations, and facilitates picking. These systems offer flexibility, scalability, and integration with pick-to-light systems, enhancing overall warehousing efficiency.
Go-Fer Bot AMR AS/RS
Go-fer bot AMR AS/RS, a unique type of automated storage and retrieval system, uses autonomous mobile robots that move on the floor, lift shelving racks, and transport them to pick stations. These systems offer flexibility in handling various inventory types, including totes, boxes, pallets, and garments. They also provide high-density storage, high throughput, and high ROI.
Stacker-Bot Case Shuttle AMR AS/RS
Stacker-bot case shuttle AMR AS/RS uses autonomous mobile robots that extract totes or cases from shelves within the warehouse and deliver them to conveyors or workstations. These robots can interleave storing and retrieving activities, making them suitable for agile, high-density, and cost-effective goods-to-person systems within a warehouse environment.
Carousel-Based AS/RS
Carousel-based AS/RS, a versatile example of an automated storage and retrieval system, uses rotating bins to provide access to requested items. Two types exist: horizontal carousels (rotating horizontally) and vertical carousels (rotating vertically). These systems are commonly used for small items, parts, documents, and raw materials.
Robotic Horizontal Carousel AS/RS
Robotic horizontal carousel AS/RS consists of multiple tiers of carousels with an inserter/extractor device, showcasing advanced technology for automated retrieval. The device retrieves totes or cartons and delivers them to a conveyor for transport to workstations. These systems offer scalability, allowing capacity to be increased by adding carousel rows.
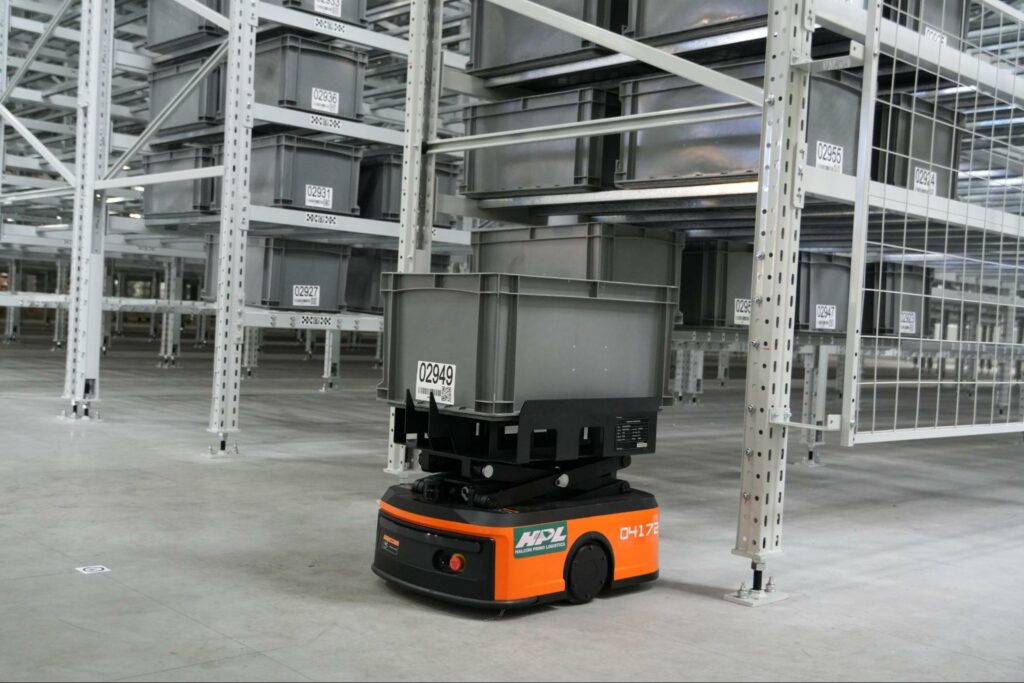
Halcon Primo Logistics: Optimising Your Warehousing with AS/RS
Halcon Primo Logistics is a leading provider of end-to-end logistics services and understands the importance of efficient warehouse storage. We are dedicated to continuous innovation and investing in cutting-edge technologies to provide our clients with the most effective solutions.
Our upcoming state-of-the-art bonded warehouse, expected to be completed in April 2025, will feature advanced AS/RS capabilities. If you are interested in learning more about what AS/RS can do for your business, contact Halcon Primo Logistics today to optimise your warehouse operations.