Efficient warehouse operations are crucial for success in today’s dynamic and competitive business environment. In order to meet the demands of modern commerce, optimise the supply chain, and achieve business goals, warehouse automation offers the potential to significantly enhance efficiency, productivity, and accuracy in logistics operations.
By understanding the different types of warehouse automation systems available, businesses can choose the automation solutions best suited to their specific needs and challenges. This guide will explore some of the most popular warehouse automation technologies and their applications.
Automated Dimensioning Systems
Automated dimensioning systems capture precise measurements of parcels and pallets, which is crucial for efficient storage, handling, and shipping. These systems eliminate manual measurement errors, leading to inaccurate billing and wasted warehouse space, and streamline data capture for improved inventory management.
This automation is particularly valuable in high-throughput distribution centres and e-commerce fulfilment operations where large volumes of goods are processed daily.
Automated Parcel Dimensioning Systems
These systems use technologies like infrared sensors, cameras, weighing scales, and barcode scanners to measure the dimensions and weight of parcels automatically. They can handle parcels of varying shapes and sizes, improving accuracy, efficiency, and data capture in shipping and warehouse receiving operations.
This type of warehouse automation solution is particularly beneficial for e-commerce businesses and courier companies that handle a high volume of parcels with varying dimensions. By automating the dimensioning process, these businesses can optimise packaging, reduce shipping costs, and improve order fulfilment speed.
Automated Pallet Dimensioning Systems
These warehouse automation systems capture the dimensions and weight of pallets, including irregular-shaped ones. This data is essential for optimising pallet loading, storage, and transportation, especially in high-volume pallet handling operations. By accurately capturing pallet dimensions, businesses can maximise storage space and improve truck loading efficiency, reducing transportation costs and overall supply chain efficiency.
This technology is particularly valuable for manufacturers, distributors, and wholesalers who handle large quantities of palletised goods.
Goods-to-Person (GTP) Technologies
Goods-to-person (GTP) technologies optimise picking and packing processes by bringing goods directly to the operator, eliminating the need for extensive walking and searching within the warehouse. This improves picking accuracy, reduces labour costs, and increases overall efficiency.
GTP systems are especially beneficial in warehouses with high order volumes and a wide variety of SKUs, such as e-commerce fulfilment and retail distribution centres. There are many different types of GTP systems to choose from, depending on the specific needs of the warehouse. Common types of GTP systems include:
- Carousels: Rotating shelves that bring items to the picker. Carousels are ideal for small to medium-sized items and can significantly improve picking efficiency in high-density storage areas. They are often used in e-commerce fulfilment and retail distribution centres where order accuracy and speed are paramount.
- Conveyors: Automated systems that move goods to picking stations. Conveyors can transport goods over long distances and are often integrated with other automation technologies, such as sortation systems and robotic pickers. They are commonly used in large warehouses and distribution centres to move goods between different areas, such as receiving, storage, and shipping.
- Vertical Lift Modules (VLMs): Automated storage and retrieval systems that deliver trays of goods to the operator. VLMs maximise vertical space and are ideal for storing small to medium-sized items with high retrieval frequency. They are often used in manufacturing, healthcare, and retail environments where space is limited and efficient storage is crucial.
Automated Guided Vehicles (AGVs)
Automated guided vehicles (AGVs) are driverless vehicles that navigate within the warehouse using technologies like magnetic strips, floor markers, wires, or lasers. They are commonly used for material handling and transportation within the warehouse, automating tasks such as moving pallets or transporting goods between different areas. This frees up human workers for more complex tasks and improves safety by reducing the risk of accidents involving forklifts or other manual handling equipment.
AGVs are particularly useful in manufacturing and production environments where repetitive material movement is required. However, AGVs have limitations, such as their fixed paths and suitability for less complex environments.
Autonomous Mobile Robots (AMRs)
Autonomous mobile robots (AMRs) are similar to AGVs in that they are used to move materials around a warehouse or facility, but they are generally more intelligent and flexible than AGVs. This is because they typically use advanced sensors and artificial intelligence to navigate dynamically within the warehouse, adapting to changing environments and working safely alongside humans.
AMRs can be used for various tasks, including picking, sorting, and transportation, depending on the specific configuration and attachments of the AMR. They are ideal for dynamic environments where flexibility and adaptability are crucial, such as e-commerce fulfilment centres and warehouses with seasonal peaks in demand.
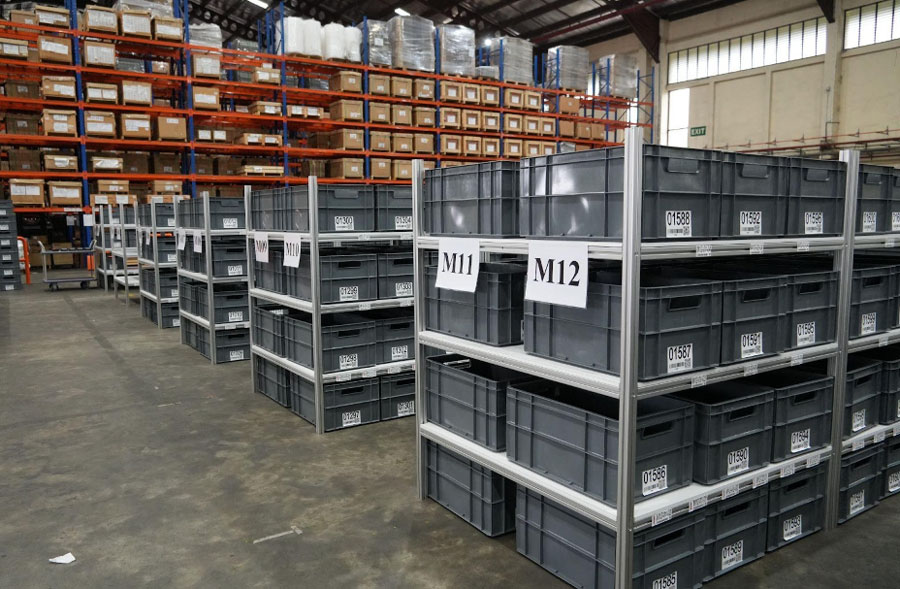
Automated Storage and Retrieval Systems (ASRS)
Automated storage and retrieval systems (AS/RS) automate the storage and retrieval of goods in a warehouse. AS/RS systems (which will be featured in our bonded warehouse) optimise space utilisation, improve efficiency, and enhance accuracy in warehouse operations.
These systems utilise cranes, shuttles, or other automated mechanisms to move goods to and from storage locations with high precision and speed. Typically, AS/RS systems involve high-density racking systems with aisles between them where the automated cranes or shuttles operate. Goods are stored in bins, trays, or pallets, and the AS/RS system automatically retrieves the required items when needed.
This type of warehouse automation solution is particularly beneficial for high-volume warehouses with limited floor space, such as those found in the food and beverage, pharmaceutical, and cold storage industries. Different types of AS/RS include:
- Unit-load AS/RS: Handles large unit loads like pallets.
- Mini-load AS/RS: Handles smaller loads like totes or cartons.
- Micro-load AS/RS: Handles very small items.
Drones
Drones, also known as unmanned aerial vehicles (UAVs), are emerging as a valuable tool in warehouse automation. While still in the very early stages of adoption, drones present exciting potential for improving efficiency and safety in warehouse operations. They can be used for various tasks, including:
- Inventory Management: Drones can scan inventory using barcode or RFID technology and provide real-time data on stock levels, improving accuracy and reducing the need for manual counting. This is particularly useful for large warehouses with high shelves or challenging-to-access storage areas.
- Inspection: Drones can inspect hard-to-reach areas, such as high shelves or racking systems, identifying potential safety hazards or maintenance needs. This can help prevent accidents and ensure a safe working environment.
- Security: Drones can monitor the warehouse for security breaches or safety hazards, providing an extra layer of surveillance and enhancing overall security measures.
Automated Sortation Systems
Automated sortation systems automatically sort and route products based on various criteria, such as destination, product type, or order priority. They use technologies like barcode scanners, RFID readers, and optical sensors to identify and direct items to the correct location within the warehouse. Automated sortation systems improve efficiency, accuracy, and reduce manual handling in distribution centres and warehouses.
This type of warehouse automation system is particularly beneficial for businesses with high-volume sorting needs, such as e-commerce fulfilment centres and parcel delivery companies.
Halcon Primo Logistics: Your Partner in Warehouse Automation
As a leading logistics company in Singapore, we understand the importance of efficient warehouse operations. We are constantly improving our service offerings to enhance your warehousing experience. Our bonded warehouse will feature advanced automation capabilities to further enhance our service offerings by April 2025. This upgrade to our facility represents our commitment to innovation and providing cutting-edge systems that empower our clients to achieve their business goals.
With our warehousing expertise and new facilities, we will ensure the right warehouse automation solutions are in place to boost efficiency and meet the demands of various sectors. Contact Halcon Primo Logistics today to learn how we can help you transform your operations.